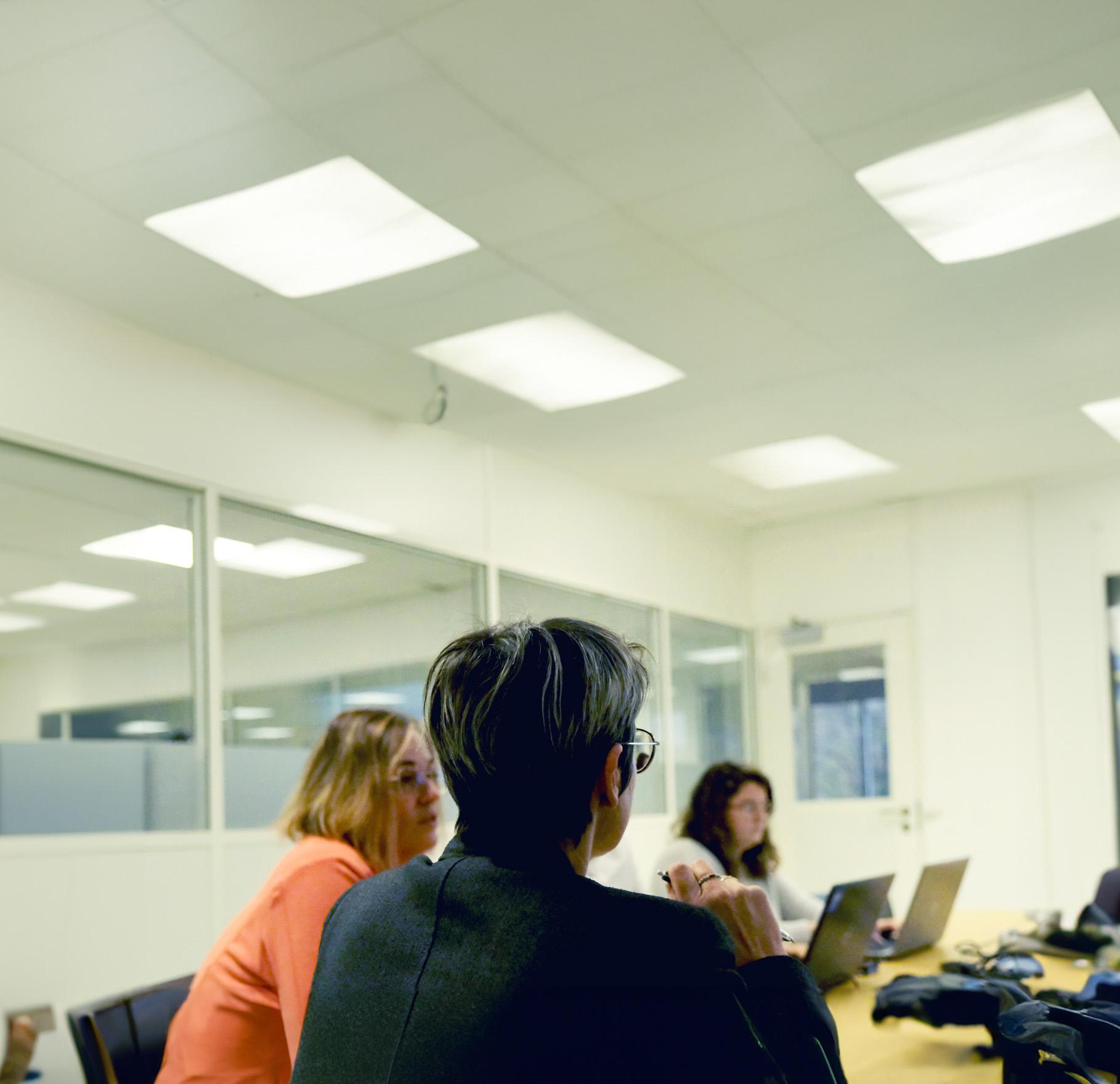
Supplier Management and Evaluation
A long-term relationship relies on fluent and efficient interactions.
Therefore the Amphenol Socapex purchasing team is monitoring suppliers performance regarding :
Quality
Defective Parts Per Million received (PPM) : this indicator reflects the number of defective parts detected (by Amphenol or his customers) out of the total amount of parts received.
Supplier Non-Conformity Rate (S-NCR %) : this indicator reflects the number of Non-Conformity-Reports raised versus the number of Purchase order lines being delivered
Delivery
OTD in-Full 1st Promise date (OTD-IFP) : this indicator reflects the Percentage of lines being delivered in full on time versus the initial promise date. This indicator is associated to the average depth of late lines.
OTD in full wanted date (OTD-IFW) : this indicator reflects the Percentage of lines being delivered in full on time versus the wanted date. This indicator is associated to the average depth of late lines.
Price
Purchasing Price Variation (PPV-Index) : this indicator help us monitoring the unit price variation.
Service
Number of open 8D & Related average time for Corrective Action plan completion : this indicator help us feeling the reactivity level of the supplier.
The ideal solution is:
- 1 Day to issue RMA
- 1 Week to confirm the defect
- 1 Month to send the corrective action plan
Supplier evaluation
The goal of this system is to provide the best products and services to our customers, to evaluate suppliers in more details and more accurately, and finally to conduct changes in our corporate structures and strategies to success, hand in hand with our suppliers and partners in global sourcing.
In order to live up to our top goal of customer satisfaction as the leading supplier of connectors, we require high quality and highly reliable sourcing partners, who are able to provide full service at a competitive price, thus helping us to meet and surpass the high demands of our customers.